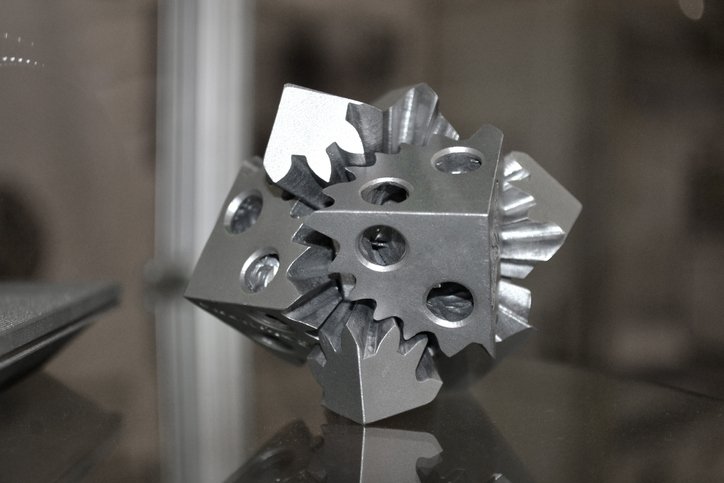
Much like people in general, manufacturing evolves. We now use better, smarter tools than our ancestors. Manual machining has been mostly phased out in favor of CNC machining.
Now, some 3D printing leaders think they’ve got the technology that will start to replace CNC/precision machining. Is that true? It depends on what you need.
CNC Machining Vs. 3D Printing: What is Precision CNC Machining?
CNC machining is the process of using a CNC (computer numerical control) machine to shape a part. It’s a subtractive process, which makes you take a larger piece of raw material and “whittle” it down — just with a machine that costs six figures rather than a pocket knife.
A CNC machine includes a carousel that holds all the tools that will be used to make a part. Your manufacturer programs the CNC machine using CAD models, and the machine does the work as programmed.
CNC was a new technology in the 1990s and was priced accordingly, but today CNC machining is the standard and very cost-effective for most applications.
Precision machining takes the concept a step further. It’s an advanced form of CNC machining that’s held to a higher standard.
- Tolerances with a CNC machine are typically 0.008” or 0.005”
- Tolerances in precision machining can be as close as 0.0001”
That little boost provided by precision machining technology allows your manufacturer to make complex shapes impossible with standard CNC or hand machining. It’s an important distinction for mission-critical products.
What Is 3D Printing?
A 3D printer takes what you designed in your modeling software and forms a part using an additive process. It prints the part using just the amount of material you need. Instead of cutting metal away as an ice sculptor would, it’s like you’re building a snowman from scratch.
3D printing is becoming popular for niche medical equipment and aerospace components because those parts sometimes require unique shapes. You may be able to mold and case them, but you can’t machine them.
For example, if you need to make a sphere with a design feature in the middle, there’s no way to get inside with CNC tooling to shave it down — unless you drill a hole in it. But with 3D printing, you can print that inner design feature in the early stages before completing the sphere.
The ability to make hollow parts ties into the other main use of 3D printing: creating lightweight components.
You can make hollow parts with a 3D printer that would be difficult or impossible with a CNC machine. With printing, you can layer the material — whether metal, plastic, or something else — in ways that reduce the amount of material required. The benefits of lightweight materials are most obvious in aerospace and medical manufacturing. Aerospace parts need to be light to conserve fuel, and medical implants shouldn’t weigh down their users.
You’ve Made Points for Both … but Which Is Better?
There’s no cut-and-dried answer to this question. You’ll have to examine several factors of production.
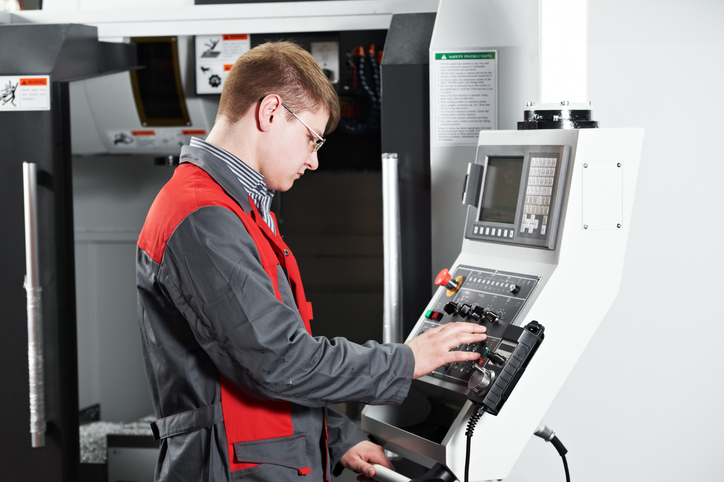
1. Cost-effectiveness
CNC machining cost is largely independent of volume. It has a much higher rate of scrap waste but is still much cheaper than 3D printing. When it was new, CNC machining was expensive, but that was decades ago — so don’t let your initial hesitance be a barrier today.
3D printing’s usefulness is dependent on volume – it can only produce a low volume effectively. The cost per unit of a given output is always the same, regardless of quantity.
It’s very expensive to 3D print today, but like most processes, it’ll probably become cheaper in the future.
2. Quality/Accuracy
High precision CNC machining is unmatched in accuracy – down to 0.001”, regardless of material. Material is not heated or reformed, so it retains strength and other properties important to your cause.
3D printing is not nearly as accurate. The material is layered, making it less structurally sound and unwelcome in high-stress settings. Those specifying 3D printing must explain the intended use of their part so the operator can choose the best build orientation.
3. Speed
A high precision CNC machine is fast, will run for hours on end, and can produce high volumes.
3D printing is the polar opposite. When it comes to subtractive vs. additive manufacturing, additive is always slower. A part that would take under an hour via CNC could take several hours on a 3D printer.
However, if you need quick prototyping, 3D printing is actually more efficient. 3D printing can also change production jobs quickly, so speed should be considered on a case-by-case basis.
4. Finishing
With CNC machining, finishing is a one-shot deal. It eliminates unwanted burrs and edges. The components may require some surface finishing and smoothing, but all of that is carried out in the machining process.
With 3D printing, finishing is a lengthy, complex job requiring multiple steps.
5. Versatility
CNC machining can produce tools, fixtures, prototypes, and more. These machines can take on just about any metal and plastic.
3D printing is limited by the materials you can use. The industry is mostly focused on manufacturing plastics right now, although metal additive manufacturing technology is developing rapidly.
Conclusion
For now, 3D printing is geared toward very specific applications. A decade from now, things may be different.
The time will come when 3D printing machines won’t even need an operator on standby — he or she will simply throw in the powder, and the part will come out completed.
While that sounds awfully exciting, CNC machining still makes the most sense for most applications — even many medical device and aerospace projects. Some forward-thinking precision machining suppliers have plans to evolve into offering 3D printing as well. But the technology still has a way to go before it comes close to the efficiency and effectiveness of CNC precision machining.
If you have any other questions about either process, click here to ask.